从加工头发,上马针织内衣,到发展起针梭织服装全功能产业链,乃至现在涉足医用材料、智能制造、全球领先的技术创新……65年经营和跋涉,位于青岛市即墨区的即发集团有限公司,一举成为全国品种最全的发饰品和中国大型纺织服装制造基地。今年虽然受疫情影响,但5-6两个月的营业收入,实现了逆势增长。
这个一直在传统行业打拼的老企业,何以能长盛不衰?
“一路打怪”
如果把困难比作“怪”的话,即发正是靠“一路打怪”发展壮大的。
即发始建于上个世纪五十年代中期,初为一家农村档发合作社,七十年代时发展为加工头发的集体小厂。1974年,因国际化纤假发开始突飞猛进发展,中国国内的人发行业受到严重冲击,即发果断压缩档发生产的出口,上新品种的生产线,加快行业拓展。劳保手套、教习假发、玩具假发、男女假发等系列新产品一举打入国际市场,企业经济效益直线上升。
1981年初,受出口配额的限制,当初把企业从生死线上拉回来的主导产品劳保手套一度停产,企业又一次面临生死存亡。即发又办起了即墨第一个“三来一补”项目,发展起了针织内衣加工产业,从传统单一的发制品行业跨越到纺织行业,企业一跃成为即墨市产值利税大户。
1993年,即发又先后与包括世界500强企业在内的多家日本商社成立了合资公司,并于2000年建立了针织工业园,带动起即墨市上千家针织产业集群。2002年12月,即墨市被中国纺织工业协会评选为“中国针织名城”。
2005年,关税贸易壁垒和人力资源问题成为困扰即发进一步发展的又一个“怪”,即发实施了“走出去”和“走进去”战略。“走出去”就是到海外建厂,他们先后在越南、柬埔寨等国家建立了研发、面料、成衣全产业链制造基地。“走进去”即把生产主体和市场主体向安徽、山东中西部等内陆地区延伸,使产业布局和内销市场进一步优化。目前,即发的产品已从过去的90%出口,调整到60%出口,国内国外两个市场逐步趋向均衡。
近年来,随着纺织订单开始由少品种大批量转向多品种小批量,传统的制造模式已难以完成这种订单,即发又开始向智能制造转型。2016年,即发将其旗下的青岛贵华针织有限公司,进行了智能化改造,用信息化打通了全产业链所有环节,建立起了敏捷制造、柔性生产的供应链模式,以快速满足多品种小批量快反应订单的市场需求。“过去一年不到40个订单,一个订单几十万件,现在每年有近6000个订单,一个订单多的几千件,少的只有上百件,有的甚至一件,而且客户要求一两个周就出货。”青岛贵华针织有限公司总经理孙维法告诉记者,“如果按照过去的制造方式,这些单根本接不了,智能制造模式下,我们不但能接得下,运营效率还提升了30%。”
在一次次成功打“怪”中,即发发展成为拥有30多个公司和分厂、2万余员工的大型企业,生产针织和梭织面料及服装、发饰品、床上用品等系列产品,出口日本、美国、欧洲等30多个国家和地区。2019年,即发实现营业收入112.29亿元,彰显着一个老行当迸发的“新活力”。
技术引领
即发能够“一路打怪”成功,离不开其较强的综合创新研发优势。即发在中国较早建立了全国针织行业首家“国家级企业技术中心”,是国家科技部认定的“国家创新型企业”和“高新技术企业”。同时,还兴建了经中国合格评定国家认可委员会(CNAS)认证的“纺织材料检测中心”,能够按照美国、日本、欧盟等多项标准实施监测。
与此同时,即发不断推进“校企财智合作”,先后与中国海洋大学、青岛大学、北京服装学院、东华大学、青岛农业大学、中科院海洋研究所、山东省纺织科学院等国内十几个高校和科研院所,以及韩国高丽大学(Korea University)、日本东丽株式会社、旭化成株式会社等国外大学和强业建立了长期稳定的合作关系;在纺织新材料、高分子材料、现代农业、医疗器械等领域的协同创新方面,取得了显著成效。
即发自主研发的“海洋生物甲壳质纤维”,就是全球第一个从自然界提炼并研发成功的抗菌防臭功能纤维。过去内衣产品抗菌防臭材料的应用,都是从化学物品提炼的,能不能从对人更有益的天然物品中提取呢?2002年,即发开始了从虾蟹等甲壳质中提炼抗菌防臭材料的研发。经过艰苦的技术攻关,2003年,即发研发的“海洋生物甲壳质纤维”终获成功,并获得国家科技进步二等奖。“当年这种新材料,在日本纺织界引起很大反响,用这种纤维生产的抗菌防臭功能的内衣,广受日本市场欢迎。”即发集团总经理杨为东介绍说。
自此,即发集团在甲壳质纤维的研发上持续发力:2010年完成了科技部国家科技支撑计划项目——甲壳素纤维纺织材料加工技术课题;2012年承担了国家科技部国际合作专项——医用甲壳素纤维材料联合开发;2012年12月,研发的“高吸液型壳聚糖纤维及医用纤维”经专家鉴定,“项目总体技术上达到国际先进水平,其中产品质量达到国际领先水平”……即发集团目前在甲壳素纤维领域获得了6项国家发明专利、2项国外PCT专利。“目前我们研发的甲壳素纤维伤口愈合、止血等医用材料已在日本、英国等国家得到了广泛应用。”杨为东说。
即发在智能型服装的研发上,也走在行业前列。“我们判断,智能化未来将是服装的标配,”杨为东告诉记者,即发通过与日本东丽、日本NTT、中科院软件研究所合作,实现了纤维与传感器、算法、无线通讯的融合,已经研发出了多种智能型服装。“我们已经研发出了可用于监测运动员运动状态、消防员身体状态的服装,还研发出了用于老年人居家养老身体监测的服装,将在未来适当时机推向市场。”
颠覆传统
2019年7月31日,中国纺织工业联合会组织专家对即发集团研发的超临界CO2无水染色项目进行了鉴定,专家一致认为:项目总体技术水平达到国际领先水平。纺织联合会还把这项技术定义为建国以来纺织行业十大颠覆性技术之一。
“无水染色技术的研发始于2014年,当时青岛地区大旱,极度缺水,纺织企业用水量很大,我们预感到水将是制约即发进一步发展的瓶颈,便开始了无水染色技术的研发。”即发集团副总经理万刚说。
上世纪八十年代,德国等欧洲国家对以二氧化碳为介质的无水印染技术进行了数十年的研究和探索,但仅限于实验室验证。上世纪九十年代,我国东华大学等也对该项技术开展了研究,至今国内外在产业化进展上仍未获得实质性突破。
2014年,即发集团通过产学研合作形式对无水染色技术组织了技术预研,对相关装备、工艺、染料匹配,以及其中的科研风险开展了研究,开始了该技术的研究与应用,并建设了连续正常运行的无水染色小试装备。“我们自主研发了数十个核心部件,与传统的纺织机械完全不同,许多部件国内外无人能做,与我们合作的主要是高端装备企业,完全是一个全新的领域。”万刚说。
经过6年时间的研发,即发先后在小试和中试中都实现了设备连续正常运转,该项目产品各项指标均达到国家相关标准,节能减排效果显著,具有良好的市场前景和社会效益,具备了产业化向前推进的条件。2021年春节前,100万件成衣规模的产业化设备也将投入运行。“整个研发过程耗资超亿元,实验3000多次,目前已递交了41项专利申请,获批23项,在日本、欧盟也已获得专利授权,美国的专利申请正在受理中。”万刚告诉记者。即发超临界CO2无水染色技术产业化的成功,对我国纺织产业意义重大。据悉,我国纺织行业废水年排放量为25亿吨,其中印染废水约20亿吨,所产生的废水必需经过处理后排放。这种“先污染、后治理”的“末端治理”模式治理代价高、难度大,企业缺乏治理污染的主动性和积极性,已严重制约了该行业的可持续发展。
“工信部已把这项技术列入2019年绿色印染指导目录,这项技术的产业化未来将具有良好的发展前景,并将带来无水染色装备业的崛起。”万刚告诉记者,国际市场基于对环境友好产品的支持,对采用这项技术生产的产品格外青睐。“法国以及日本客户都表示,无水染色的纺织产品,有多少他们要多少,并且愿意给予更高的采购价格。”
2、第一纺织网转载的所有的文章、图片、音频、视频文件等资料的版权归版权所有人所有,本网站采用的非本站原创文章及图片等内容无法一一和版权者联系,如果本网站所选内容的文章作者及编辑认为其作品不宜上网供大家浏览,或不应无偿使用(涉及费用问题,需要删除“不宜上网供大家浏览,或不应无偿使用”)请及时用电子邮件:martin@setways.com通知我们,我们会在第一时间删除,避免给双方造成不必要的经济损失。
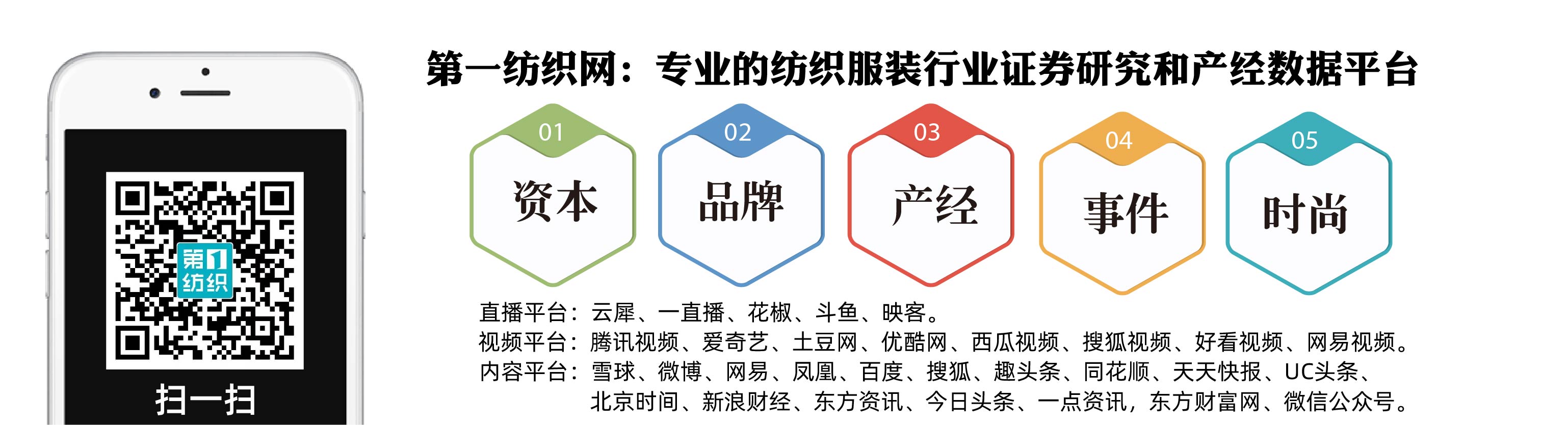
