众所周知,深黑色色变,特别是色变浅、泛红等都严重影响了印花产品的质量,有的时候还会造成整批产品降等,危害性非常大。解决的直接办法就是选择耐碱性好、固色率高、深度易提升的稳定性活性黑,这是最理想的。
活性深黑色印花色变现象的解决实践
金属质感分割线
浙江富润印染有限公司 傅国柱 俞振中 宣海地
如果由于各种原因使用了耐碱性偏差的深黑染料,我们就必须深入研究在具体生产中如何避免或减少这种色变现象,关键在于用各种办法控制碱剂用量,降低水解现象发生。
活性染料印花是最为常见的织物印花方法,它具有较高的湿处理牢度和摩擦牢度,匀染性好,色泽鲜艳,成本低,应用广泛。但活性染料的固色率不高,一般以印浅、中色为主,其中乙烯砜型及双活性基型活性染料也可以印得比较深的颜色,特别是应用最广泛的黑色,随着科学技术的不断进步,其应用也越来越成熟。
1、色变现象产生机理
活性深黑色印花色变原因要从染料的活性基说起,根据活性基团的不同,活性染料可分为均三嗪型、卤代嘧啶型、乙烯砜型、双活性基型等,其中用于印花的黑染料多为均一氯三嗪型(K型)、乙烯砜型(KN 型)、双活性基型(例如 KD型、KP型、M型、B型)。
K型黑的反应性低,而耐碱性强,稳定性高,但固色率不高。其印花的浮色多,用量大,不容易印得很深的黑色,改进后的P型黑染料在深度上有了较大的提高,其单色结构的P型黑是非常理想的印花深黑。同时要注意,市场上有很多类型的P型黑,并不是单一的母体结构,它是由几种P型染料拼混而成的,其上色性、耐碱性、稳定性都要差一点。KN型黑的反应性高于K型,容易印得深色但其耐碱性差,极易在碱性条件下水解,多用在活性黑防印印花中。双活性基黑的应用较为广泛,多为一个K 型加一个KN型的结构,其反应性比K型高,比较容易印得深色,但其耐碱性还是不尽如人意。
在实际生产中,由于价格、工艺、操作等多方面因素的影响,很多厂家在印活性深黑的时候,还是选择了耐碱性较差的KN型、B型等深黑品种。由于染料本身的原因,再加上生产过程中碱剂用量控制的不合理,使得深黑色部位或局部在碱的作用下发生染料部分水解,引起深黑色变浅、变色、牢度下降,特别是泛红现象明显。
2、色变产生的具体原因及解决
众所周知,深黑色色变,特别是色变浅、泛红等都严重影响了印花产品的质量,有的时候还会造成整批产品降等,危害性非常大。解决的直接办法就是选择耐碱性好、固色率高、深度易提升的稳定性活性黑,这是最理想的。如果由于各种原因使用了耐碱性偏差的深黑染料,我们就必须深入研究在具体生产中如何避免或减少这种色变现象,关键在于用各种办法控制碱剂用量,降低水解现象发生。
1、印花坯布前处理
前处理对深黑色色变的影响并不十分明显,毛效要求好一点,这有利于深黑色上色。有一点要注意,布面要洗干净,含碱量不能太高,特别是一些丝光的印花坯,如果去碱不充分,造成纤维内部含有烧碱,极易引起活性染料在处理过程中水解,造成印花色变浅、变色,特别是耐碱性差的深黑色尤为明显。
2、描稿的处理
印花一般为多套色构成,有深、中、浅之分,一般花型结构都有浅色压在深色上的叠色以及浅色向深色的复色处理。在叠色、复色部位,由于深黑色作最深色被浅色反复叠印,形成不同套色的碱剂在局部累加现象,造成局部碱剂含量过高而引起黑染料水解,此为引起黑色变浅、泛红的主要原因。
解决的办法主要有2种:
金属质感分割线
第一,对花型结构在描稿时一定要进行调整,能不做叠色的尽量不做叠色,浅色掏空作复色处理,为了解决对花难题,复色可多做一些360dpi单边6到8个点。即使必须用叠印才能达到效果的,浅色也可改成云纹泥点效果叠印,目的就是减少色浆中碱剂累加的机会,特别是一些花型有3至4套色叠印在一起的,更会加剧水解现象的发生。
第二,结合工艺,对黑色作分套处理。把无叠色的大块面与叠色多的小块面云纹泥点、细颈分开,这样大块面就可以用反应性高、固色率高、耐碱性差、价格相对便宜的染料品种,一些小的块面及泥点、细茎并为一套,一方面可以方便调整刮印效果,另一方面此套色可以用价格高、耐碱性强、稳定性好的活性黑印花来控制水解,例如非拼混的一氯均三嗪型类活性黑改良品种PBR黑等。有时根据生产的具体情况,此套色也可直接用涂料来代替,刮印效果好,又不变色。
3、印花工艺的合理制定
活性印花是靠碱剂来固色的,并不是说碱剂用量越多越好,碱性越强越好。反应性低,稳定性好,耐碱性能优秀的K型、P型等均三嗪类染料,碱剂用量可高一些,NaHC03为主,有时还可加用Na2C03。对于反应性高、固色率高、耐碱性较差的染料,只能用NaHC03等碱性较弱的固色剂来固色,并且用量要严格控制,达到工艺保险范围就可以了。碱剂使用除跟染料品种有关外,还要看颜色深度。
染料用量高的深色,当然碱剂的用量要高,可以用2.5%~3%。但有很多工艺制定者在制定工艺时,对颜色浅,染料用量并不高的色浆碱剂用量控制并不严,也极不科学,对低于5g/L染料用量的浅色色浆来说,一般用l%的NaHC03,保证pH值在11左右就可以了。操作中有的用1.5%,有的用2%,甚至还有人加Na2C03,这不仅加剧了浅色本身的水解,如果作为浅色叠印在深黑色上,严重造成了深色部位碱剂累加现象,引起深黑色水解泛红。
另外,对尿素的用量也要科学地制定,深色多加点尿素是可行的,10%-l2%,视具体情况而定。叠印的中、浅色尿素用量不能高,P型中浅色用6%-8%就可以了。尿素用量过高,特别是叠色部分,在蒸化时就会局部过度吸收水份,引起染料水解加剧。
4、色浆的配置
这条对于控制深黑色水解泛红是至关重要的。
首先,用料用量要严格按工艺执行。工艺制定多次就加多少,工艺制定加什么就加什么,切忌操作人员私自调整,否则发生质量事故时,工艺制定者查都无法查起。
第二,原浆要充分膨化、搅匀。原浆的不均匀,会导致碱剂局部分布不均匀,有的地方碱浓高,容易引起水解色变现象。
第三,化染料时,不能直接向染料注入95℃以上的开水。这极易引起染料结构变化,造成色变,应先用冷水或温水搅成糊状,再慢慢注入热水逐步溶解。
第四,海藻原浆的配制,有的厂家称备用糊。有时为了方便操作,往往会在打原浆时就加入碱剂,对于深色PK型色浆还可再追加一部分碱剂,但对于PK型浅色及含有KN型或双活性基类染料的色浆就有问题了,PK型浅色可用Na2C03作碱剂,但千万不能多,加入60-70%海藻原浆的色浆中,纯碱含量要有2%左右明显高了,这增加了被叠印的深黑色碱剂累加程度,最后使叠印部分你黑染料水解变色。建议浅色色浆还是用NaHC03作为碱剂比较安全,也可配备两种原浆备用。KN型、双活性基的B型等染料色浆,不要用碱性较强的Na2C03作为固色剂,如果统一使用已预加了Na2C03的原浆,就增加了自身发生水解色变的几率及叠印部分碱性太强。
第五,加了碱剂的色浆要尽快使用。染料的水解与碱性强弱、pH值、温度、时间都有关系,加了碱剂的色浆如果长时间不用(例如大于l2h),就会慢慢在碱的作用下使染料在印花前有部分水解,最后造成色变,很多厂家是在印花前才加入碱剂的。
5、机台刮印对色变的控制
机台刮印一般对水解变色影响不大,有两点要注意:
第一,给浆量不能多,特别是有3-4套叠色的地方,否则会加重碱剂累加,引起水解。
第二,烘干适当控制,不能过干,这对蒸化不利。也不能含潮过多,只要有水分,碱剂就可能使活性黑发生不同程度的水解。
6、蒸化、水洗环节的影响
如果生产管理不到位,影响是非常明显的。
第一,印花下机后要及时蒸化,蒸化后要及时水洗。因为只要没有把碱剂充分从布面洗净去除掉,由于布的吸湿,印在布面上的色浆总是或多或少地带有一定的水份,促使染料在碱剂的作用下慢慢地被水解,累积多了,也会发生色变。
第二,蒸化保证一定的湿度对固色非常有利,但如果湿度过大,叠印的深色部分尿素又过量,就会引起水份过度聚集,从而加重水解。因此,活性蒸化要保证一定的湿度,又不能过度,由各个工厂根据生产的具体情况而制定不同的湿度控制参数。
第三,水洗一定要净,水洗烘干后布面不应再有碱剂存在,以pH=4.5-7.5为宜。如果不洗净,虽然布面含碱量已经很小了,但是在后期加工仓储、销售、服用过程中,由于发生布面少量碱剂长期的微水解现象,也会使黑色发生色变而泛红。有很多印染厂出厂时布面的色光是正的,没有色变泛红等现象,但过了几个月后,有时也有布面深黑色色变泛红的,这或多或少与布面去碱不彻底有关。
7、新工艺的研究
为了解决深黑色染料因碱剂过量而色变泛红这一现象,很多技术人员在这方面进行了研究。比如先轧处理液再印花,所谓的处理液就是碱剂、防染盐S、尿素、海浆等按一定的比例配好,过轧车打底。打好底的布印花时,一般中浅色的色浆里就不用再加碱剂,从而杜绝因印花叠印造成的局部碱剂累加,一定程度上解决了深黑色色变难题。处理液中碱剂的品种及用量,根据不同的操作方法有所不同,有的只用Na2C03,有的用NaHC03、Na2C0的混合液,用量从2%-6%不等,有时会用的更多。也有人从轧焙烘、湿短蒸等工艺着手研究解决这种现象。
3、总结
在实际生产中,由于各种因素的共同作用,有时发生活性深黑等染料在碱剂作用下被水解的现象是无法完全避免的。但只要我们抱着科学的态度,钻研的精神,务实的行动,从各个方面加强管理,严格操作,不断追求工艺进步,一定能很好地解决这个难题。我们也希望随着技术的进步,染料厂家能开发出活性适中、固色率更高、稳定性更好、能印出特深色的系列活性染料。
2、第一纺织网转载的所有的文章、图片、音频、视频文件等资料的版权归版权所有人所有,本网站采用的非本站原创文章及图片等内容无法一一和版权者联系,如果本网站所选内容的文章作者及编辑认为其作品不宜上网供大家浏览,或不应无偿使用(涉及费用问题,需要删除“不宜上网供大家浏览,或不应无偿使用”)请及时用电子邮件:martin@setways.com通知我们,我们会在第一时间删除,避免给双方造成不必要的经济损失。
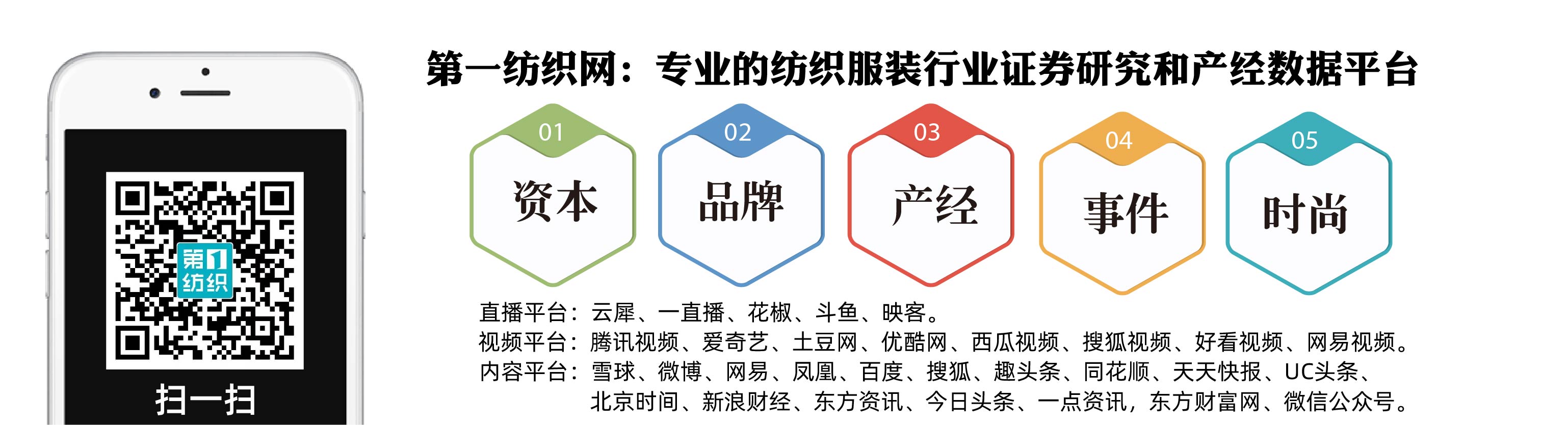
